Alger gir bedre og mer miljøvennlige batterier
Tekst: Anne-Lise Aakervik
Foto: synlig.no
Det startet som en idedrodling over en kaffekopp – om noen år kan batterier produsert ved hjelp av alger, stå i den neste elbilen eller ferja som går over fjorden.
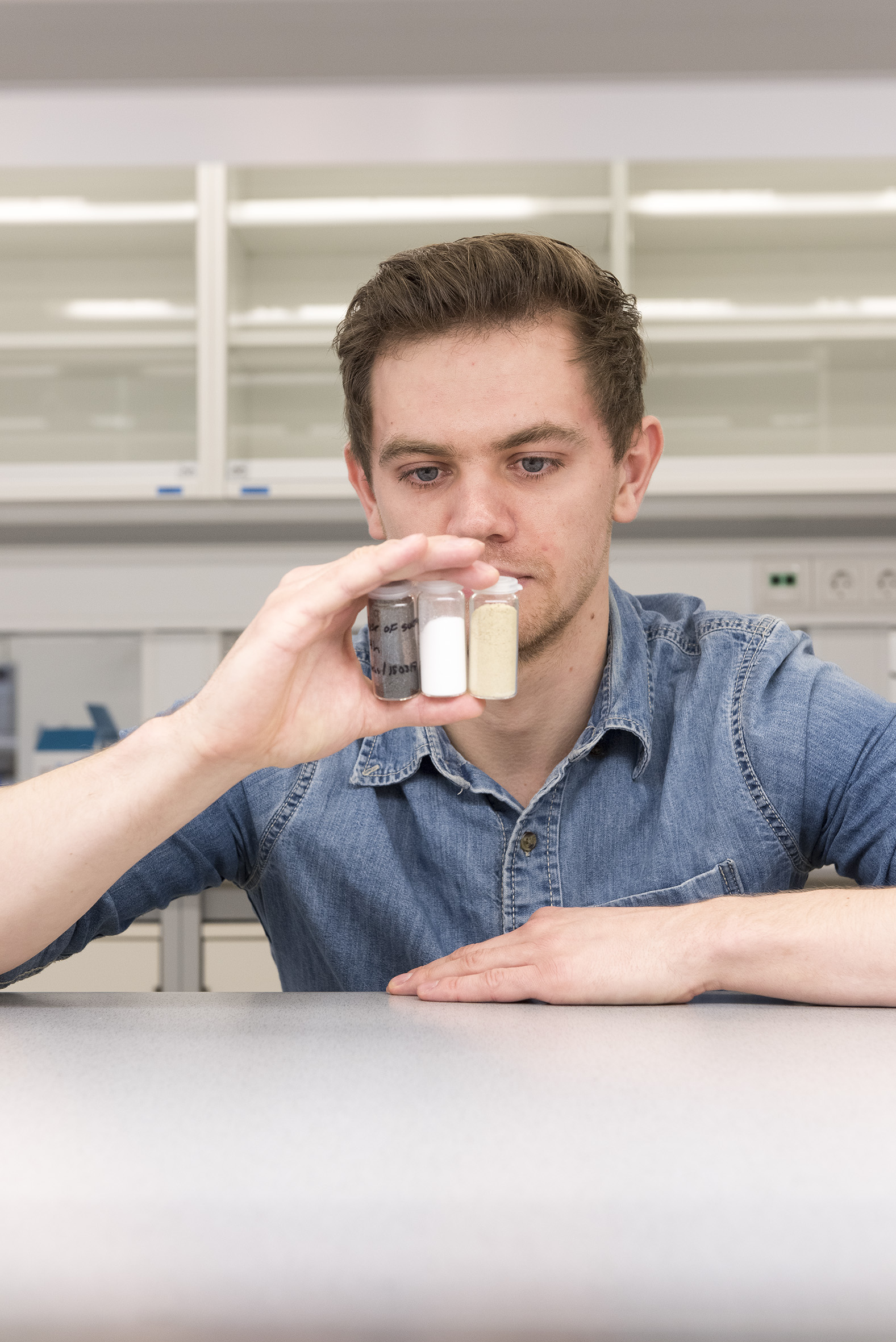
Forskere fra Institutt for Materialteknologi har funnet en løsning for å forbedre den negative enden i litium-ionebatteriet, anoden, betydelig. Det nye anodematerialet som inneholder alger, har høyere kapasitet og er mer miljøvennlig å produsere, det vil ha lengre levetid og større ytelse.
Fride Vullum-Bruer hadde vært på et møte, og ble sittende å drodle sammen med en kollega om bruken av alger i energiproduksjon. – Vi hadde hørt om et prosjekt der alger ble brukt i solcelleproduksjon for å samle lys, men det fungerte ikke, fordi det var så mange utfordringer knyttet til bruken av algene. Vi ble inspirert av dette allikevel, og jeg begynte å ta det inn i forskningen min på batteriteknologi.
Nå har teamet fått tildelt penger fra NTNU Discovery for å teste materialet i en full-celle batteri prototype. – Midlene er avgjørende for å kunne løfte teknologien videre til neste steg, sier Susanne Jäschke som er prosjektleder fra TTO. Og prosjektet har fått et navn: Diatoma.
Dette teamet ønsker å ta ny batteriteknologi ennå et skritt videre. Fra venstre prosjektleder Susanne Jäschke fra TTO, Entrepreneur-in-Residence Kristin Lønsethagen, gründer Andreas Norberg og oppfinner Fride Vullum-Bruer.
Høyere kapasitet, grønn og billigere
Den største utfordringen man står overfor når det gjelder dagens anodemateriale, er at ytelsen har nådd sitt maksimum – hvor mye energi de kan lagre. Dagens batterier er flaskehalsen i det grønne energiskifte som skjer over hele Europa. Nye materialer er påkrevd for at kvaliteten skal bli bedre. I tillegg er dagens materialer lite miljøvennlige. Det vanligste råmaterialet er grafitt, enten basert på fossile resurser, eller kunstig fremstilt med et stort CO2 fotavtrykk. Det benyttes også farlige kjemikalier under produksjon av batterielektrodene, og de høye kostnadene gjenspeiler seg i sikkerhetskravene som stilles ved produksjon av disse elektrodene.
– Så når vi nå introduserer en bedre, billigere og mer miljøvennlig anode ved å benytte et fornybart råmateriale, som samtidig har høyere kapasitet enn det som er kommersielt tilgjengelig i dag, så har vi løst flere utfordringer med dagens teknologi på en gang, sier Fride Vullum-Bruer og smiler.
Vidunderalger
Så hva er det med algene som gjør dette mulig? Disse algene vokser både i fersk- og saltvann og er en fornybar ressurs. De har en naturlig nano-struktur som vi utnytter i batterielektrodene uten mye videreforedling.
Vanligvis bruker man år på å kopiere naturens nano-strukturer i laboratoriet, men her kan vi la de gå rett inn i prosessen. I tillegg brukes det et bindemiddel i elektroden, som muliggjør bruk av vann som løsemiddel istedenfor giftige stoffer som i dagens batteriproduksjon. Sluttproduktet vil derfor inneholde langt mindre farlige stoffer enn tidligere og har et mye mindre CO2 fotavtrykk enn dagens anodemateriale.
Fride Vullum-Bruer sendte patentsøknaden allerede i 2015. – Etter at medoppfinneren og post-docen min flyttet tilbake til hjemlandet sitt, hadde vi ingen til å jobbe videre på den tekniske siden. Det er først nå at vi har fått på plass en engasjert gründer med bakgrunn i nanoteknologi, Andreas Norberg.
Andreas Norberg har som oppgave å ta den tekniske delen av Diatoma videre med penger fra NTNU Discovery.
Industrien venter
Eksisterende industri, som produserer batteripakker til maritime anvendelser i Trondheim, er med som rådgivere og nærmest står og tripper for å teste ut teknologien.
– Vi er sånn sett i en ønskesituasjon, sier Jäschke. – På sikt har vi planer om å etablere produksjon av anodematerialet i Trondheim. Teknologien virker veldig lovende, men har fortsatt en del utfordringer som vi håper å få løst i løpet av testperioden nå fremover.
Utfordringene skal løses ved å lage en prototype av en full-celle med det nye anodematerialet og standard katode for å bekrefte at denne typen batterier har inntil 40% høyere kapasitet enn kommersielle batterier som bruker grafitt/karbon som anode.
– Vi har allerede vist at anode materialet kan lades og utlades i minst 1000 sykler, som er et veldig godt utgangspunkt for videre utvikling, sier Kristin Lønsethagen, som er Entrepreneur-in-Residence på TTO, og også har nanoteknologi som bakgrunn.
– Nå er det bare å sette i gang og påvise økt ytelse i en full-celle, avslutter Norberg.
Slik kan en testlab for batterier være.
Fakta batterier
Felles for alle batterier er at de er bygget opp av en anode som mottar elektroner, en katode som avgir elektroner og en elektrolytt som transporterer ioner mellom dem. For et oppladbart batteri er anode og katode definert ut fra cellereaksjonene under utlading. Anoden i et Li-ionebatteri består oftest av karbon. Denne gitterstrukturen er ideell for å fange et litiumatom i sentrum.
Prosjekter og nyheter
Kontakt:
Prosjektleder
Jan Hassel
Epost: jan.hassel@ntnu.no
Telefon: 906 53 180
Kontor: Hovedbygget, sokkel
Håvard Wibe
Epost: havard.wibe@ntnu.no
Telefon: 41 47 37 68
Kontor: Hovedbygget, sokkel
