NTNU Discovery tildeler millionbeløp til innovative forskere
Ny revolusjonerende ultralydteknikk. En smart sensor som automatisk overvåker tilstanden til elektriske maskiner. Torsdag 9. november delte NTNU Discovery ut én million kroner hver til to lovende innovasjonsprosjekter utviklet av forskere og ansatte ved NTNU og Helse Midt-Norge.
Tekst og foto: Per-Steinar Moen
Toril Hernes, prorektor for nyskapning på NTNU, stod for utdelingen av midlene til hovedprosjekt i Gruva, NTNUs innovasjonshub. Denne gangen var det to utvalgte prosjekter som slapp gjennom nåløyet av totalt 11 søkere til NTNU Discovery hovedprosjekt.
– NTNU Discovery har faktisk delt ut 120 millioner kroner siden 2011, og det er fordelt på 400 prosjekter. Det er ganske mange dyktige fagfolk både på NTNU og i Helse Midt-Norge. I dag gjør vi ære på både på de som søker på NTNU Discovery, men også de som får midler, sier hun.
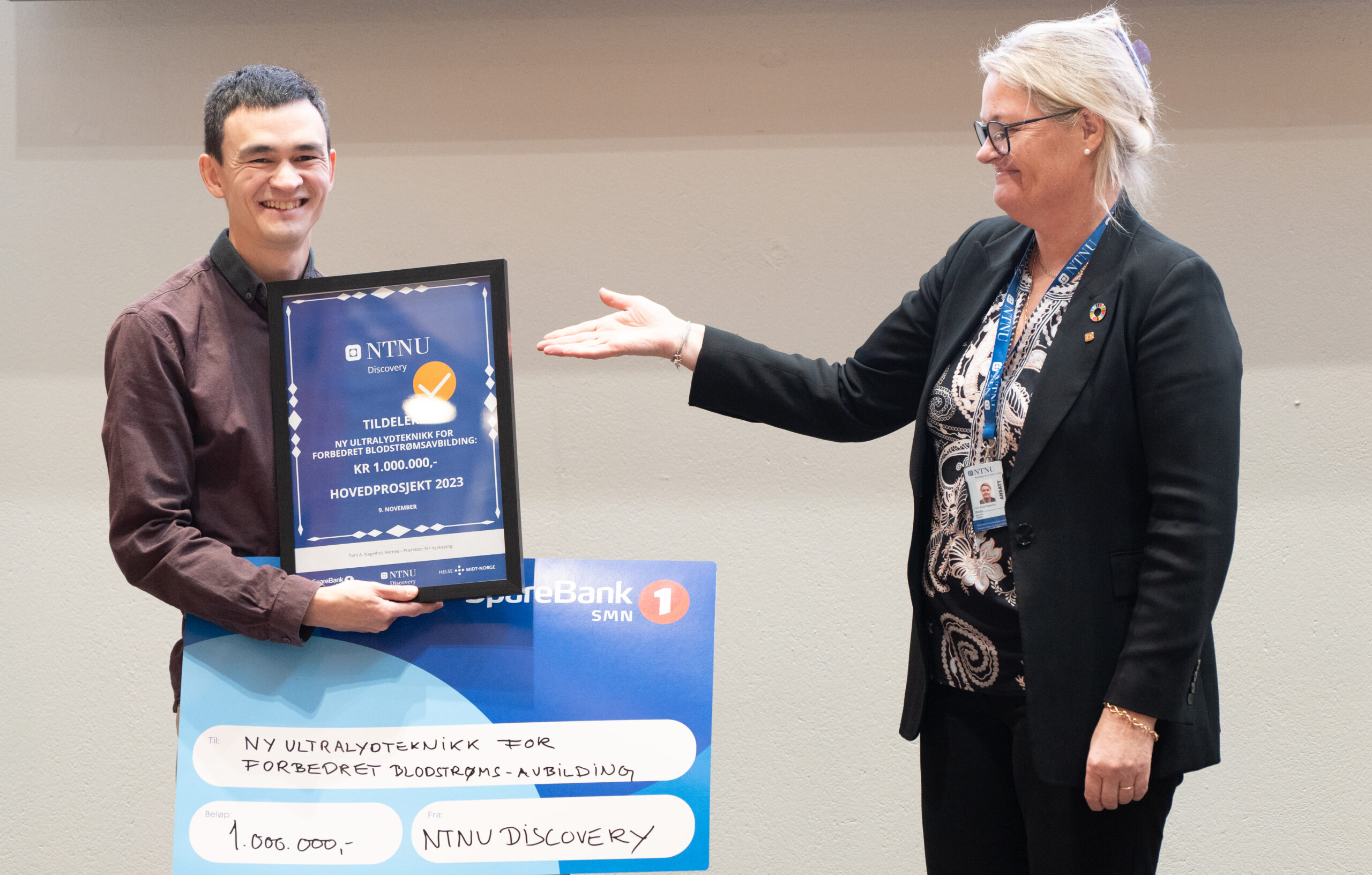
Jørgen Avdal mottar en millioner kroner til hovedprosjektet fra prorektor for nyskapning, Toril Hernes.
Revolusjonerende ultralyd
Den første millionen ble gitt til prosjektet FVD (Flow Vektor-Doppler), ledet av Jørgen Avdal og Ingvild Kinn Ekroll ved Institutt for sirkulasjon og bildediagnostikk og med deltakere fra Helse Midt-Norge og industripartneren GE Healthcare.
FVD er en ny ultralydteknikk for avbildning av blodstrømmer som vil gjøre det enklere å diagnostisere hjerte- og karsykdommer.
– Prosjektet viser at de er langt framme med et innovativt produkt, de løser et problem og gjør noe nytt hvor det kommersielle elementet er til stede. De har kommet langt med verifikasjon av teknologien, som stammer fra det verdensledende ultralydmiljøet på instituttet, sier Hernes på vegne av juryen.
Enklere og mer effektiv diagnostikk
Ultralydmålinger av blodstrømshastigheter brukes i dag blant annet til å vurdere hvilke pasienter som vil ha nytte av en operasjon for å redusere risiko for hjerneslag. På grunn av de svært høye blodstrømshastighetene som kan oppstå i områder med karsykdom, har det frem til nå vært vanskelig å automatisere disse målingene, noe som gjør at utfallet av en undersøkelse til en viss grad er operatøravhengig. FVD er en revolusjonerende teknikk som gjør at ultralyd også kan brukes til å måle svært høye blodstrømshastigheter, som gjør at de diagnostiske målingene blir mer nøyaktige og lettere å reprodusere.
Forskere har i 30 år sett på muligheten for slike målinger, men nå står kanskje ultralydmiljøet på NTNU og Helse Midt-Norge foran et lite paradigmeskifte. Dagens teknologi klarer nemlig ikke å måle hastigheten på blodstrømmene presist når blodet går fort. Og en viktig indikator på at pasienten utvikler en hjerte- og karsykdom er nettopp at hastigheten på blodstrømmen går fortere.
– Ultralydoperatøren må i dag gjøre mange manuelle valg underveis i en undersøkelse. Dette er tidkrevende og innfører også variabilitet i målingene. To forskjellige operatører kan komme til ulik konklusjon for en og samme pasient. Løsningen vår vil gi veiledning om riktig posisjonering og vinkling av proben. Når operatøren har plassert proben riktig, kan ultralydmaskinen fortelle hvor de høyeste blodhastighetene er og gjøre automatiserte målinger. Slike målinger har hittil ikke vært pålitelige, sier Avdal.
Automatisk deteksjon
Ved hjelp av avansert signalbehandling og matematiske analyser vil FVD-programvaren gi klinikeren tilgang til langt mer detaljert og målbar informasjon enn hva som er mulig i dag, slik som automatisk deteksjon og graderinger av innsnevringer i blodårene. I tillegg til å komme pasientene til gode ved å gi et sikrere beslutningsgrunnlag for diagnose og behandling, vil teknologien gi bedre arbeidsflyt for de som gjør undersøkelsene og være tidsbesparende i klinikken.
Målet med hovedprosjektet er å tilrettelegge teknologien for kommersielle systemer gjennom en klinisk pilotstudie, forbedre brukergrensesnittet og etter hvert utvide teknikken til flere bruksområder, slik som hjerteavbildning og fosterdiagnostikk.
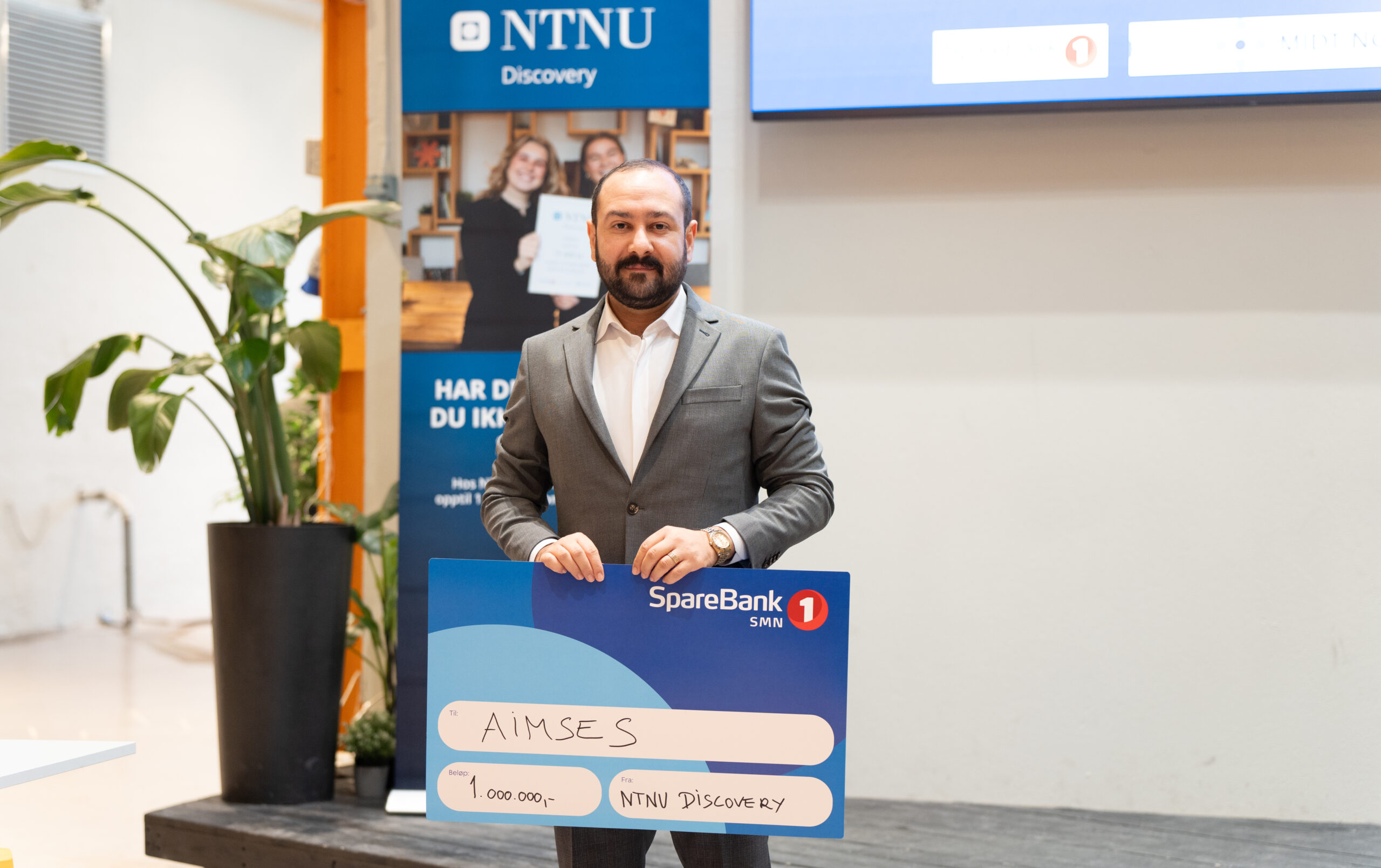
Hossein Ehya ved Institutt for elektrisk energi.
Enklere overvåking av elektriske maskiner
Elektriske maskiner og motorer utgjør en stadig større del av vår hverdag. Nordmenn kjøper stadig flere elbiler, som fraktes av de første elektriske fergene over fjorden og det er planer å elektrifisere deler av flyparken også. AIMSES er et nytt overvåkingssystem for elektriske systemer som på et tidlig stadium kan oppdage feil på alt fra store generatorer i vannkraftverk og vindparker til elmotorer i transportsektoren.
– AIMSES har kommet langt og viser at det er et potensial for produktet i markedet. Industrielle aktører har vist interesse, de har utviklet et pilotprodukt og viser tydelighet i sin forståelse av markedet, skriver juryen i sin begrunnelse.
AIMSES ledes av forsker Hossein Ehya og professor Arne Nysveen ved Institutt for elektrisk energi på NTNU. Produktet har vært i utvikling siden 2018 og har de siste årene vært testet i flere norske vannkraftverk. De har tidligere fått innvilget 200 000 kroner fra NTNU Discovery forprosjekt og fem millioner kroner fra Forskningsrådet for å se på verifikasjon og kommersialisering.
Det finnes sensorer for å måle tilstanden på slike maskiner på markedet i dag, men utfordringene er at de ofte må installeres inne i selve maskinen (med påfølgende nedetid) og er avhengig av gode historiske data for å finne terskelverdiene for når systemet skal melde fra at noe er galt. AIMSES er langt enklere.
Fra dager til sekunder
– Fordelen med AIMSES er at vi kan redusere inspeksjonstiden fra dager til sekunder. Sensoren kan installeres på utsiden av maskinen, slik det er ikke nødvendig å stanse driften under installasjonen. Med hjelp av kunstig intelligens får vi detaljerte opplysninger om type feil, hvor feilen er lokalisert og om maskinen bør stanses. Algoritmene våre kan brukes i alle elektriske maskiner til alle bruksområder uten at vi trenger historiske data. Systemet gir også detaljerte analyser til sluttbrukeren, som ikke trenger å gjennomgås av eksperter, sier prosjektleder Hossein Ehya.
Enklere installasjon uten nedetid, samt bedre data for når det er behov for vedlikehold og eventuell utskifting, vil på sikt gi betydelige besparelser ved å bruke AIMSES, mener forskerne bak sensoren og programvaren.
AIMSES har vært testet ut i flere norske vannkraftverk, men teamet ser for seg langt flere bruksområder, blant annet innen elektriske transportsystemer, vindparker og olje- og gassnæringen.
Hossein Ehya sier at støtten fra NTNU Discovery skal brukes til å kommersialisere produktet. Målet er å etablere selskap i løpet av 2024 og levere produktet til markedet i 2025.
Andre nyheter
Nye millioner til ansatte og studenter
Stor prisutdelingskveld med tildeling av hovedprosjektmidler fra NTNU Discovery under arrangementet Tech, Hugs and Rock’n’Roll på Digs torsdag 5. juni.
Femten minutters bedømmelse
Du får femten minutter til å overbevise juryen i NTNU Discovery om at ditt prosjekt er verdig støtte til hovedprosjektmidler.
Kontakt:
Prosjektleder
Jan Hassel
E-post: jan.hassel@ntnu.no
Telefon: 906 53 180
Kontor: Hovedbygget, sokkel
Håvard Wibe
E-post: havard.wibe@ntnu.no
Telefon: 41 47 37 68
Kontor: Hovedbygget, sokkel
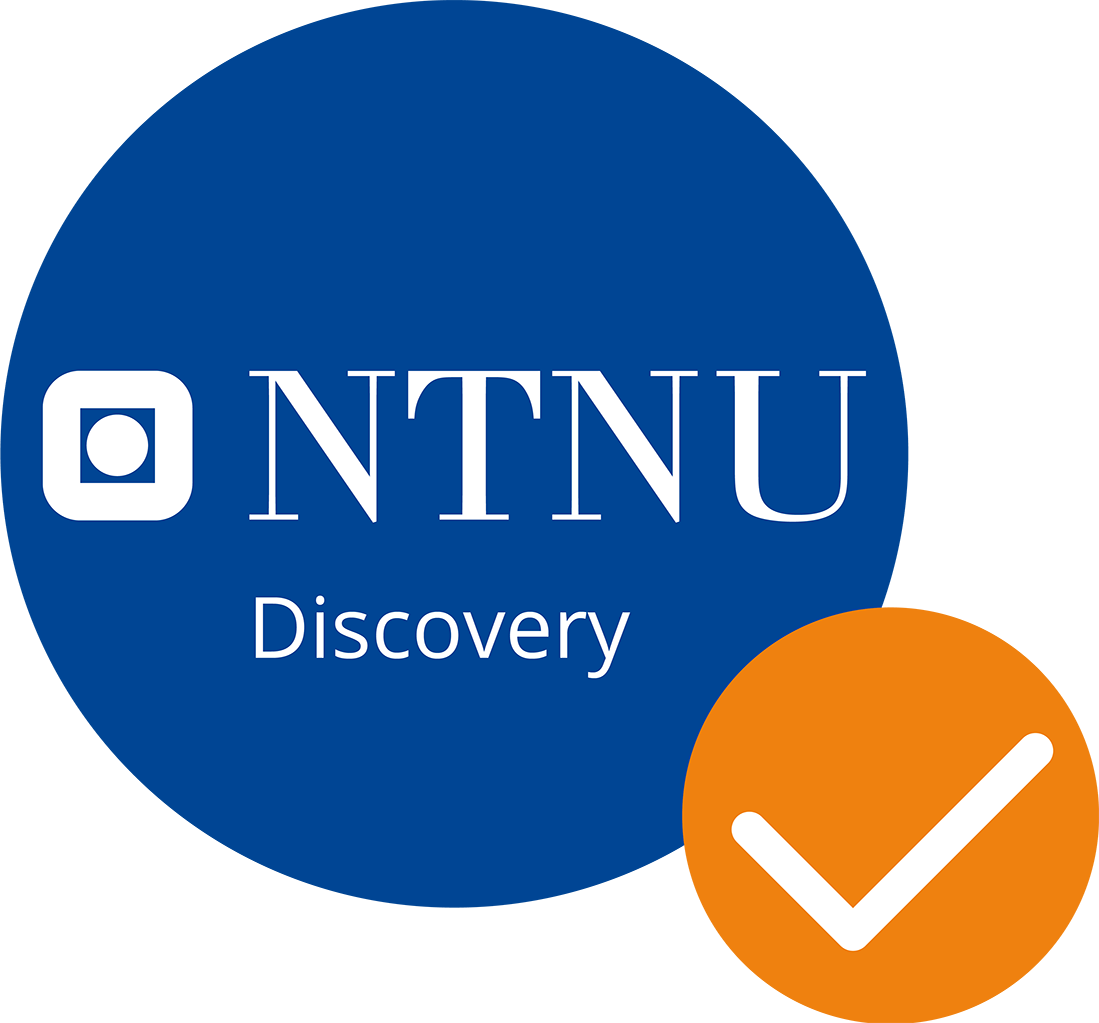
Ta idéen din videre
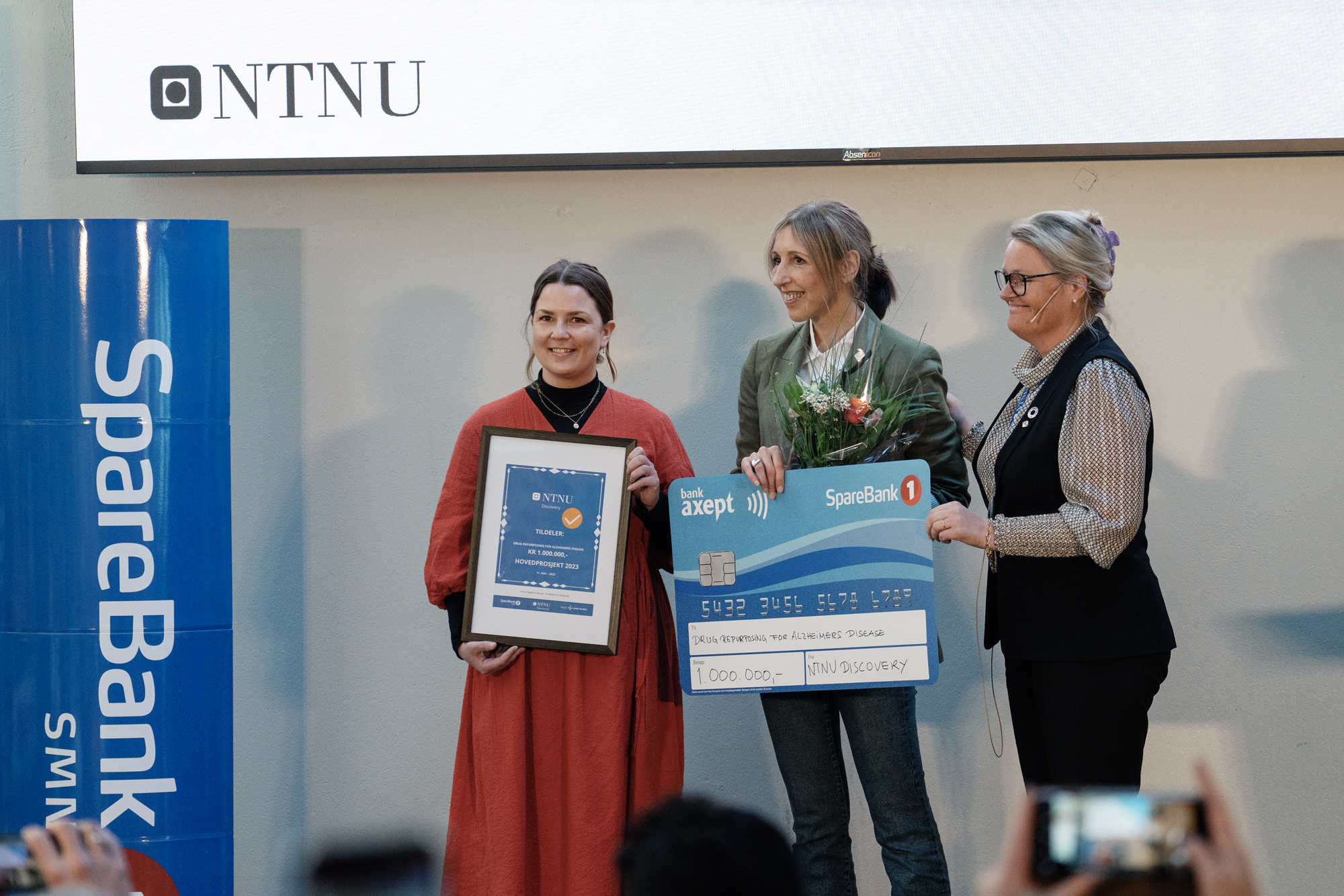